產品設計,就是用最低的成本,滿足客戶最低的需求。說白了,就是在產品功能剛好達到客戶要求的前提下進行「偷工減料」。
產品設計必須透過業務(客戶),結構工程師,電氣工程師,五金模具工程師,塑膠模具工程師,注塑工程師,設備工程師,實驗室,原材料廠商等各單位的通力合作,在每一個環節滿足客人需求/產品功能,在每一個環節「偷工減料」。
下面我們來研究一下手機連接器產品中的塑膠產品設計。
塑膠產品的設計與其他材料如鋼、銅、鋁、木材等的設計有些是類似的;但是,由於塑膠材料組成的多樣性,結構﹑形狀的多變性,使得它比起其他材料有更理想的設計特性;特別是它的形狀設計、材料選擇、製造方法選擇,更是其他大部分材料無可比擬的。因為其他的大部分材料,其設計者在外形或製造上,都受到相當的限制,有些材料只能利用彎曲﹑熔接等方式來成形。
塑膠產品的設計,我們的考量點有:
a. 產品的功能?外觀要求/應力負載/使用環境
b. 模具加工?
c. 成型特性?
d. 組裝方式?
一、外觀要求/應力負載/使用環境
板端的產品一般沒有外觀要求,但線端會有。第一是顏色,第二是表面處理。
深色的塑膠在成型製程上比淺色的好控制,不容易產生色差,而且在組裝製程,包裝過程,包括客人的後加工製程,都不易受污染。純黑色是一個很好的選擇。業務可以建議客人採用。
表面處理主要是指產品的表面粗糙度,一般有鏡面處理和咬花處理。塑膠產品的鏡面處理一般在模具上實現(有些外觀件的鏡面處理是通過塑膠產品的表面電鍍來達到)。在模具製造上,模具工件要進行表面鏡面拋光,使得模具在製造和後續模具維護困難;在成型製程中對成型參數的穩定性要求高,模具工件因磨損而修整或重做的頻率高;因表面縮水或塑膠產品的內應力會導致外觀不良,在結構設計時也需考慮,盡量通過結構調整來避免;在組裝製程/包裝過程,包括客人的後加工製程容易刮花,損耗高。所以需表面鏡面處理的塑膠產品成本會比表面咬花處理的成本高得多。但即使在生產過程中被小心翼翼地保護的塑膠產品鏡面,我估計到消費者手上後不到1分鐘就會被刮花,對於消費者而言,這些鏡面並沒有實用價值,只是「花瓶」,而消費者則要為這個「花瓶」付出更多的成本,個人認為是非常不值得的。
一般手機連接器上的塑膠產品都不會有工作應力負載,但在結構上如果有過盈配合,則會在製程過程產生應力負載,所以設計上我們仍然要做一些調整來滿足。
壁厚均勻是塑膠產品設計的第一原則。特別是對於尺寸較大的產品。因為壁厚不均會產生不均勻收縮或縮水,並且壁厚不均就會有結構突變,突變的地方就會產生內應力,而收縮不均和過大的內應力會導致翹曲。塑膠產品的冷卻時間取決於壁厚較厚的部分,壁太厚使成形週期延長,生產效率降低。板端類的產品因產品結構關係不能做到壁厚均勻,但也需在某些壁比較厚的地方進行偷料。產品外形盡量採用流線外形,避免突然的變化,以免在成形時因塑膠在此處流動不順引起氣泡等缺陷﹔並且此處模具易產生磨損。
同時可以用以下方法加強結構,防止在製程過程產生的應力負載產生變形﹕
1. 轉角部位加R
塑膠產品的尖銳轉角常常是造成產品破壞的最大因素。消除產品尖銳的轉角,不但可以降低該處的應力集中,提高產品的結構強度,也可以使得塑膠材料成形時有流線型的流路,以及成品更易於頂出。另外,從模具的觀點,圓角也是有益於模具加工和模具強度。
產品所有的內側和外側的周邊轉角圓弧都必須盡可能的大,以消除應力集中;但是,太大的圓弧可能造成縮水,特別是在肋或突柱根部轉角圓弧。
綜上所述,圓角對於塑膠產品的設計會有以下的一些優點:
a. 圓角使得塑膠產品強度提高以及應力降低.
b. 尖銳轉角的消除,自動地降低了龜裂的可能性。就是提高對突然的震動或衝擊的抵抗能力。
c.
塑膠的流動狀態將被重大的改善,圓形的轉角,使得塑膠能夠均勻,沒有滯留現象以及較少應力的流入模穴內所有的斷面,並且改善塑膠產品斷面的密度之均勻性。
d.
模具強度獲得改善,以避免模具內尖銳的轉角,造成應力集中,導致龜裂,特別是對於需要熱處理或受力較高的部分,圓弧轉角更為重要。
圓角加大,應力集中減少。
內圓角R <0 .3T--應力劇增
內圓角R > 0.8T--幾乎無應力集中
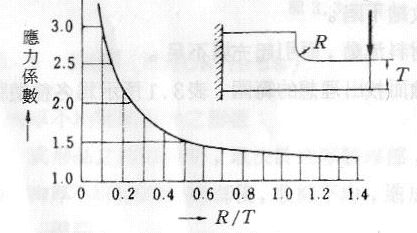
2. 增設加強肋
一般而言,板端類產品不需要加強肋,線端外殼部分會有。肋根部厚度約為 ( 0.5~0.7 ) T,肋間間距 > 4T,肋高L
< 3T。依照不同的材料會做一些調整。
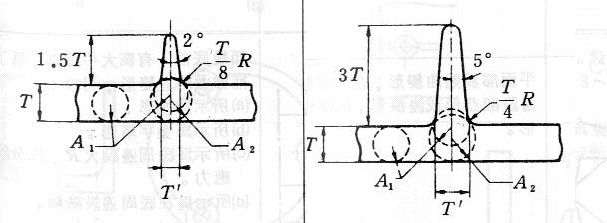
利用變化肉厚及形狀
a. 側壁加強:既可防止變形,也可改善流動性
b. 邊緣加強:用變化的邊緣形狀來加強,防止變形
c. 周邊加強:較大的平面易發生翹曲變形,用周邊凹凸或波浪形來防止變形
d. 底部加強:箱形件底部,為加強及防變形常採用如下方法:
3. 當線端類產品上下外殼採用緊配結構時,孔的設計要注意
a.
孔的高度一般不超過本身直徑的兩倍,否則必須加加強肋。(太高時會引起氣孔,燒焦,充填不足等)
b. 孔的位置不能太接近轉角或側壁,如果空間不允許,孔的一側需和側壁相連,則需注意肉厚均勻。
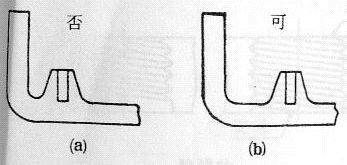
c.
孔的形狀以圓形為主,周圍可用除去部分肉厚(即開火山口)來防收縮下陷 (如下右圖)
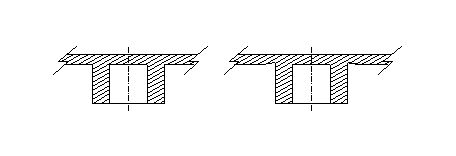
塑膠材料選擇的多樣性,使得設計工作變得更為困難,如我們所知,目前已經有一萬種以上的不同塑膠被應用過,雖然其中只有數百種被廣泛應用。但是,塑膠材料的形成並不是由單一材料所構成,而由一群材料族所組合而成的,其中每一種材料又有其特性,這使得材料的選擇,應用更為困難。
但手機連接器的使用環境比較單純,沒有苛刻的環境要求。一般低端的產品,塑膠原料我們採用比較便宜的PBT/POM/ABS等;中端的產品,塑膠原料我們採用工程塑膠,如PA/PC等;高端的產品,塑膠原料我們採用高性能工程塑膠,如LCP/PA9T等。材料的選擇需依照產品的應用,重點考量的是客人的製程。特別是板端類產品,都需滿足SMT製程的需求,所以板端類產品的塑膠原料都採用耐高溫的高性能工程塑膠。
二、模具加工
塑膠產品涉及到模具的部分,主要有以下幾點需要考量:
1. 進膠點之選定
進膠點一般採用潛伏式進膠方式,自動剪裁膠口提高成型效率。但必要時也會採用直接進膠,如2118-000-151 & 152
的鏡面蓋,以減少壓力損失,保證外觀效果。
進膠點的位置決定了塑膠的填充模式和縫合線位置。站在產品的角度來考量,縫合線位置不能在有應力負載的地方,否則容易產生龜裂。另外如果不想進膠點毛邊高於塑膠面,可以先在塑膠面上做0.1mm深度的沉孔,再放進膠點。
2. 分模線之選定
a. 不得位於明顯影響外觀的位置
b. 開模時不形成死角(undercut)的位置
c. 位於模具易加工的位置
d. 位於成品後加工容易的位置
e. 位於不影響尺寸精度的位置(尺寸關係重要的部分盡量放在模具的同一邊)
分模面必定產生毛邊。對於板端類產品而言,如果毛邊在貼近PCB的塑膠底面,會影響到端子焊腳底平整度或位置尺寸,所以塑膠底面盡量不要有分模面,如果一定會有分模面,則在結構上更改毛邊方向。對於裝配部分的結構,如果分模面毛邊影響到裝配後的尺寸,也必須在設計上做一些調整,逃開。
分模面產生錯位是另一個在產品設計時就要考量的問題,因為錯位會導致組裝困難或裝配後的產品尺寸變異,所以在塑膠產品設計上需要做一些結構避免。
3. 脫模斜度
脫模斜度是為了便於產品從模具中脫出而設置的。脫模斜度一採用1~2度,最小不小於0.5度。具體數值視成品形狀,成形材料的類別,模具結構,表面精度,以及加工方等會有所不同。在不影響產品品質的前提下,脫模斜度愈大愈好。
4. 頂針位置
因手機連接器的產品體積小,在塑膠產品設計的時候必須考量頂針位置,而頂針位置必然也會產生毛邊,在貼近pcb的塑膠底面和塑膠裝配面上要避免放置頂針,如一定要放置,也許通過一些小結構來避開。如先做一個0.1mm深的沉孔,再放頂針,來避免頂針對產品功能和裝配的影響。
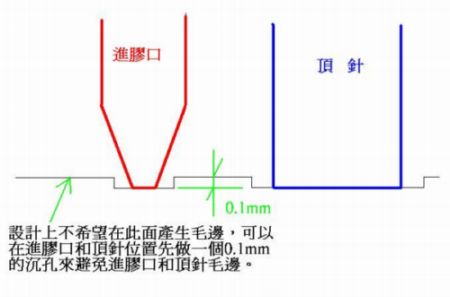
三、成型特性
塑膠產品的成形加工方法多種多樣,而手機連接器產品的塑膠件主要通過射出成型來進行塑膠加工。產品的結構決定了模具的結構,而模具的結構決定了成型的特性。在塑膠產品設計的時候需要考慮:
1.
壁厚最小部位的長度和厚度,結合材料的熔融指數來判定是否合理。一般來說厚度不少於0.25mm,否則塑膠產品在成型時會有不飽模。
2.
成型時間與產品設計/模具設計,在產品設計和模具設計的時候要考量盡量避免在模具上跑滑塊或會有其他複雜的模具結構,導致成型時間加長,效率下降,不良率升高。
3.
成型參數之確定,除了要確保塑膠產品的外觀和尺寸,還需確保塑膠產品的縫合線質量,特別縫合線的部分有應力負載的時候。可以通過增大成型壓力,提高模具溫度和熔膠溫度來提高縫合線質量。
4.
產品設計/模具設計盡量避免出現明顯的壓力降。例如不合理的產品結構設計(出現結構突變的狀況),不合理的模具流道設計。
四、組裝方式
產品設計的時候必須考量組裝製程,如何做到穩定/快速/方便。
1.
任何裝配的地方都盡可能加上R角或倒角,以便在組裝時導向
2. 採用過盈配合的裝配方式,塑膠產品在過盈配合的地方要避免產生裂紋/龜裂。
3. 塑膠產品在裝配的地方避免有毛邊導致組裝尺寸變異。 |